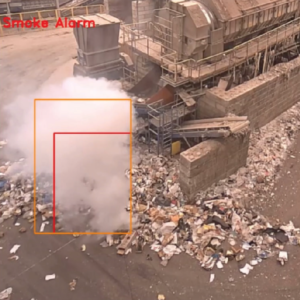
Why Is Early Fire Detection Important, and How Can It Save My Business?
Early fire detection can make the difference between a minor incident and a full-blown disaster. For businesses operating in high-risk environments, identifying a fire in its earliest stages can save